ATK’s Aerospace Structures division has been selected as the National Center for Defense Manufacturing and Machining’s (NCDMM) partner for phase 2 of a US Air Force Research Laboratory (AFRL) project.
NCDMM is under contract with AFRL to develop an automated inspection system to detect defects in aircraft components produced by automated fibre placement (AFP) machines.
ATK will now collaborate with NCDMM and Ingersoll Machine Tools, for three-month beta site implementation testing of the automated inspection system during AFP production in one of its production facilities.
NCDMM and Ingersoll are currently developing an on-tool inspection system for AFP under the phase one of the project.
NCDMM Operations Director Jim Fisher said ATK clearly demonstrated extensive AFP experience during performance assessment and has a proven track record of supporting the production and development of AFP programmes.
"Additionally, ATK is building hardware for the F-35 Joint Strike Fighter, which will allow our inspection system to be tested and compared side by side with the baseline manual inspection process," Fisher said.
How well do you really know your competitors?
Access the most comprehensive Company Profiles on the market, powered by GlobalData. Save hours of research. Gain competitive edge.
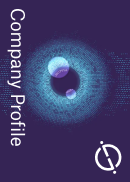
Thank you!
Your download email will arrive shortly
Not ready to buy yet? Download a free sample
We are confident about the unique quality of our Company Profiles. However, we want you to make the most beneficial decision for your business, so we offer a free sample that you can download by submitting the below form
By GlobalData"I am confident that the results of ATK’s beta testing will help us to make any necessary refinements and move closer to transitioning and implementing the inspection technology to support higher speed AFP operations."
Ingersoll president and CEO Dr Tino Oldani said, "The automated inspection system we developed has been shown to work in a laboratory test environment and we look forward to the system being proved in a more thorough production environment on actual aerospace hardware to confirm the reliability of the system."
The new automated system is expected to facilitate occurrence of inspections in real-time while the composite structure is being fabricated by alerting the operator of defects and anomalies, and their repair during the fabrication process.
The system also includes an electronic database system to electronically document and track defects.
The existing inspection practices require production to be interrupted after each ply, and manual inspection for identification of defects, such as missing or twisted tows, gaps between tows, inaccurately placed tows, bridging, wrinkles or splices, and foreign objects and debris.