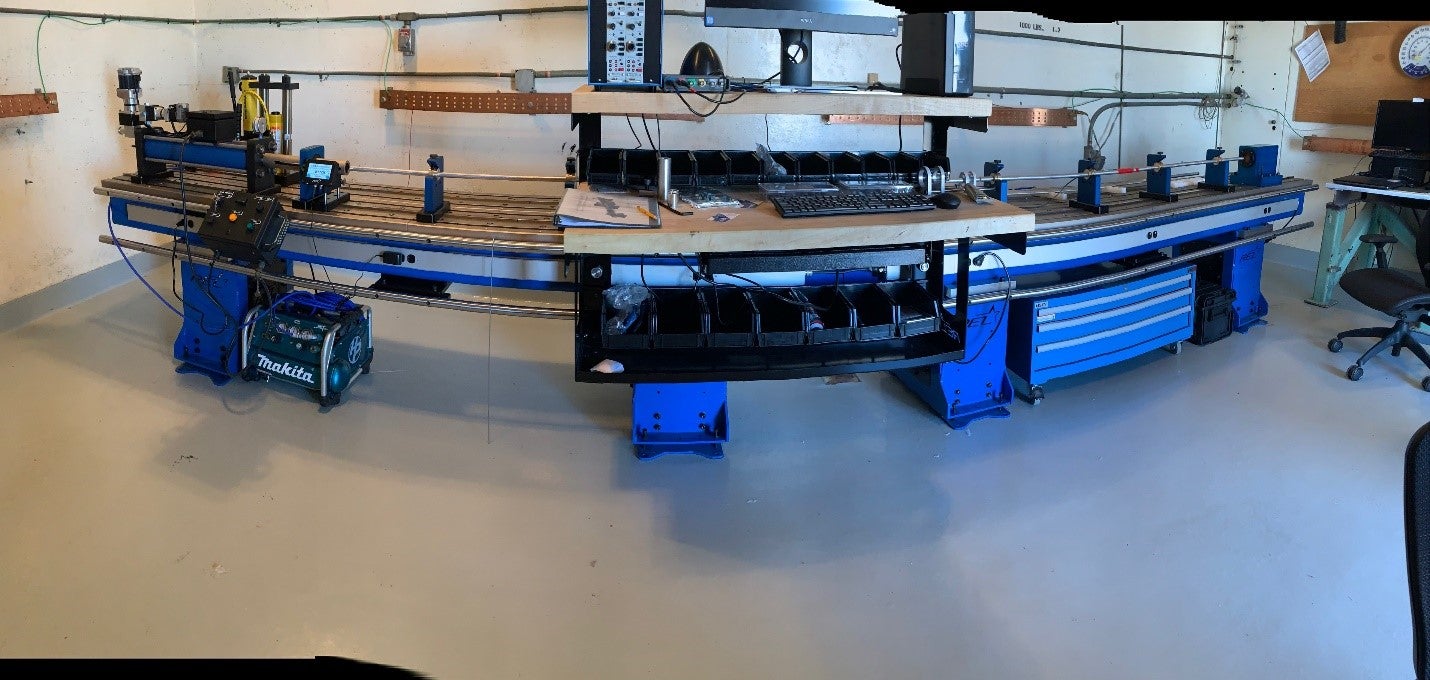
The Air Force Research Laboratory’s (AFRL) Rocket Propulsion division has unveiled the Split-Hopkinson Pressure Bar, a system to measure stress at high strain rates in a solid rocket motor.
Also known as a Kolsky bar, the equipment is designed to help evaluate material behaviour under complex conditions.
The system was installed at AFRL’s on-site chemistry lab.
Engineers from the AFRL division at Edwards Air Force Base in California will use the equipment to test and collect data from solid propellants and other space-bound materials.
According to AFRL, the system tests solid propellant at strain rates equivalent to that generated from threats such as bullet impact, fragment impact and other sympathetic detonations.
AFRL Propellant Branch senior materials research engineer Dr Timothy Miller said: “This system will give AFRL a new and unprecedented capability to test and gather data from any solid propellant we can manufacture.
“This new equipment capability will continue to propel AFRL into the future.”
Dr Miller said that AFRL would use the system to test both propellant and space-bound materials at high-strain rates.
Researchers will aim to develop structural models to predict behaviour, especially failure, in real-world conditions.
These structural models will be used to help design enhanced rocket motors and satellites, as well as investigating scenarios related to space debris impact.
According to Dr Miller, all solid rocket motors tested may have defects that are not visible during manufacturing.
Even if no defects are found on a rocket motor, it is still open to damage from other external events.
Dr Miller said: “Data from high strain rate tests is key to preventing [unintentional damage].
“AFRL will use this system to quantify material properties related to all rocket motors, including those made with advanced manufacturing processes such as Resodyn mixing and additive manufacturing.”
In March, AFRL launched a joint project with Case Western Reserve University (CWRU) to expedite the development of biosensors.
The $2m project will focus on the detection of biomarkers for stress and fatigue.