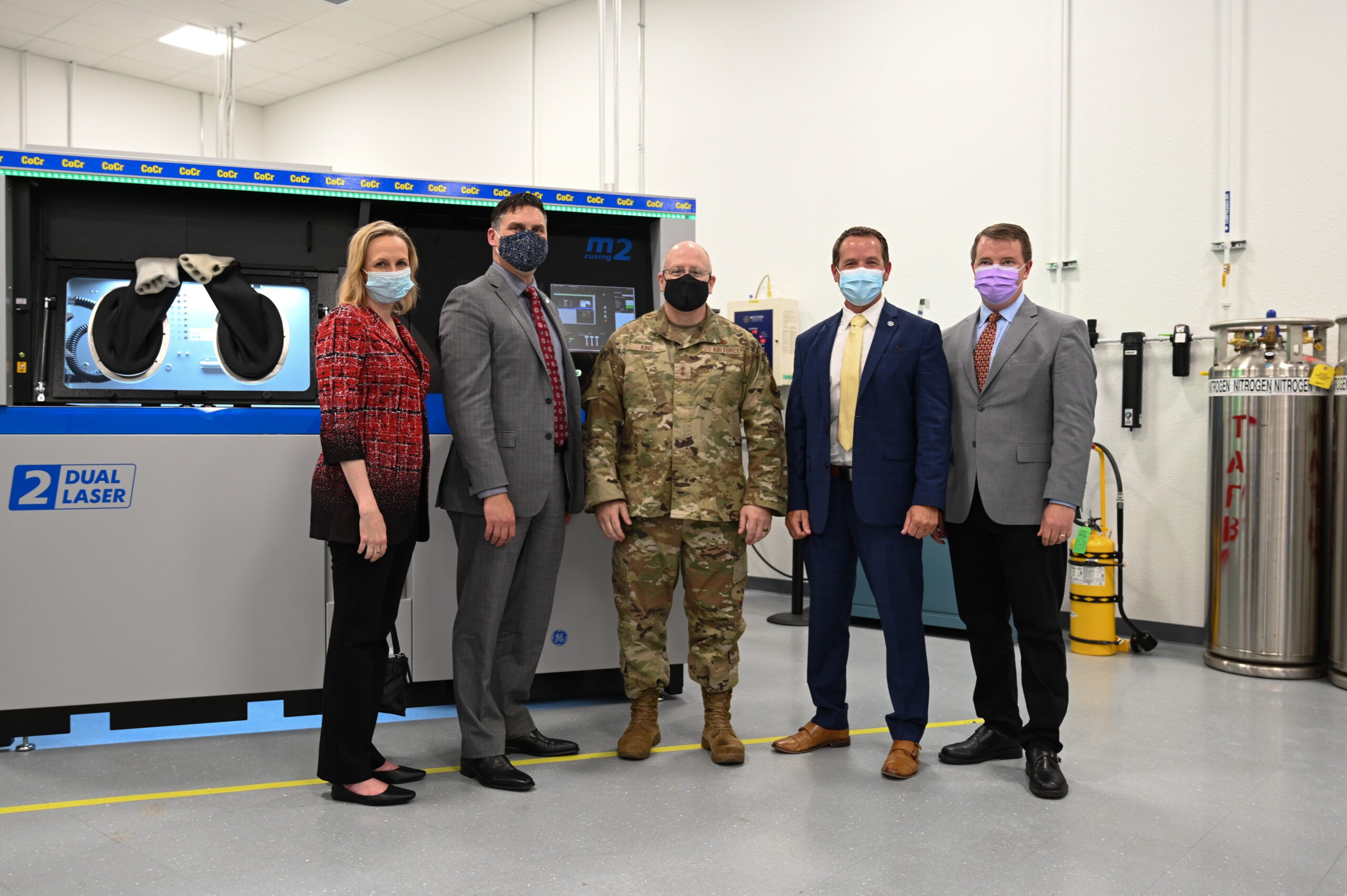
The US Air Force Life Cycle Management Center’s (AFLCMC) Propulsion Directorate and Oklahoma City Air Logistics Complex (OC-ALC) have unveiled a new additive manufacturing facility.
Known as Reverse Engineering and Critical Tooling (REACT-II) laboratory, the facility will host two 3D metal printers acquired under the US Air Force’s (USAF) Pacer Edge programme.
The opening of OC-ALC’s second lab REACT-II was marked by a ribbon-cutting ceremony.
It was attended by industry partner General Electric and various key stakeholders of the Pacer Edge programme.
The two alloy metal 3D printers will demonstrate the USAF’s capability to additively manufacture metal aircraft and engine components.
However, the flight-related parts manufactured in the lab will require safety certification from the USAF’s Airworthiness Certification Authority.
The Pacer Edge programme primarily aims to enhance the USAF’s weapon system readiness by fulfilling the needs of manufacturing, supply, and repair.
This programme is a collaborative effort of government and industry partners to deliver a technology that can reduce the cost of sustainment and increase production speed.
It has also supported the production of two engine-related airworthy metal 3D-printed parts for B-52 Stratofortress and F-16 Fighting Falcon aircraft.
More than a dozen parts are currently under different stages of development with the AFLCMC/LP and OC-ALC.
AFLCMC Propulsion Directorate director John Sneden said: “The directorate embraced additive manufacturing because of one big strategic reason that is to improve propulsion readiness for the warfighter.
“Additive manufacturing puts us in the driver’s seat so we can source those low volume hard to get parts at speed of need.”