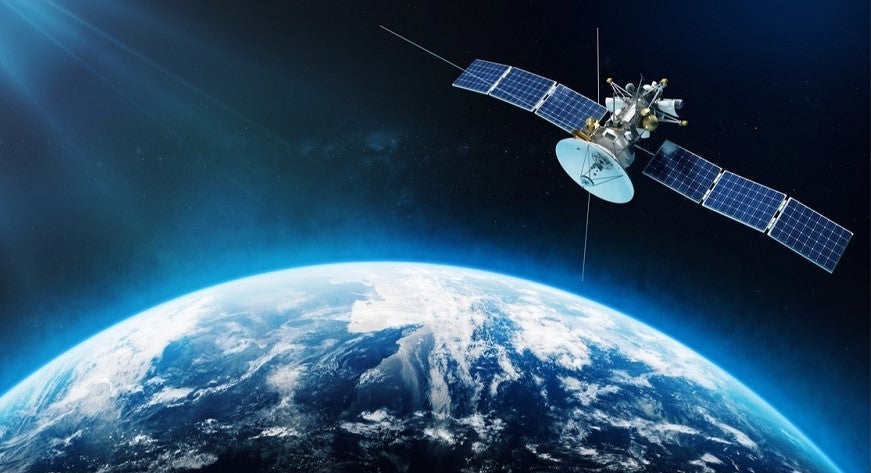
To protect TV broadcast and communication satellites, and ensure that they continue working, components such as circuits, transistors, and CPUs need to be designed, manufactured, and tested to resist high levels of cosmic radiation. Satellites that receive and broadcast TV and communication signals are placed in geostationary orbits, outside of the protection of the Earth’s atmosphere (approximately 22,000 miles up) where radiation is particularly intense. Components for these systems need to be ‘hardened’ against radiation and extreme temperatures by using insulating layers made from materials such as depleted boron.
On the other hand, protection for low Earth orbits (LEO), such as those used by the Starlink constellations (approximately 340 miles up), do not require the same radiation requirements since satellites are located within the outer atmosphere. For LEO missions, ‘radiation tolerant’ (light shielding) protection is required and used. This is an advantage for “New Space” products like CubeSats where commercial off-the-shelf technology can be applied to keep costs and weight to a minimum.
Award-winning radiation hardened and tolerant components
VPT, Inc. is a global leader in providing power conversion solutions for use in space. Organizations including NASA, ESA, Lockheed Martin, Orbital, and others regularly rely on VPT’s proven power solutions to power critical space missions and provide avionics and other high-reliability applications. With decades of proven spaceflight heritage behind them, VPT also provides standard military designs, and engineering models for fast design and prototyping.
Creating reliable power distribution systems, VPT has an array of radiation tolerant, and radiation hardened isolated DC-DC converters, radiation hardened non-isolated point-of-load converters, and radiation immune EMI filters. These are available in varying Total Ionising Dose (TID) and Single Event Effects (SEE) levels and are suitable for all orbits, such as low Earth orbit (LEO), medium-Earth orbit (MEO), geostationary orbit (GEO), and deep space or launch programs.
VPT features multiple series of innovative DC-DC converters and accessories, designed, tested, and proven for the challenging environment of space, which include:
The VSC Series – Designed as the first commercially available off-the-shelf DC-DC converter, guaranteed for radiation tolerance, and provides protection for LEO applications. The VSC series is designed to keep costs low by avoiding radiation hardened components and using surface-mounted PCB manufacturing techniques.
The SVL Series – Characterized by Total Ionizing Dose (TID) performance, including Enhanced Low Dose Rate Sensitivity (ELDRS), to 60k rad, the SVL series is operable over the full military temperature range (-55 °C to +125 °C) with no power derating, and suitable for use in low Earth orbit (LEO), medium Earth orbit (MEO), geostationary orbit (GEO), deep space missions, and launch vehicle programs. VPT recently added 50V input versions to the SVL family that offer a wide input range of 30 to 60V with an 80V transient capability for the higher voltage satellite busses that are becoming more common worldwide.
The SVR Series – The SVR series is hardened to TID: 100k rad (Si), qualified to MIL-PRF-38534 Class K, and designed for TOR compliance. These space level characterizations enable VPT to offer appropriate levels of protection suitable for use in (LEO), (MEO), (GEO), deep space, and launch vehicle programs.
The SGR Series – The SGR Series is the first commercially available GaN-Based, space-qualified line of DC-DC converters. It is radiation tolerant and achieves high efficiency up to 95% due to the GaN technology. Radiation tolerant to TID: 100k rad (Si), including Enhanced Low Dose Rate Sensitivity (ELDRS), and Single Event Effects (SEE) performance to 85 MeV/mg/cm2
All VPT products are designed and manufactured in accordance with the latest revision of MIL-PRF-38534 Class K.
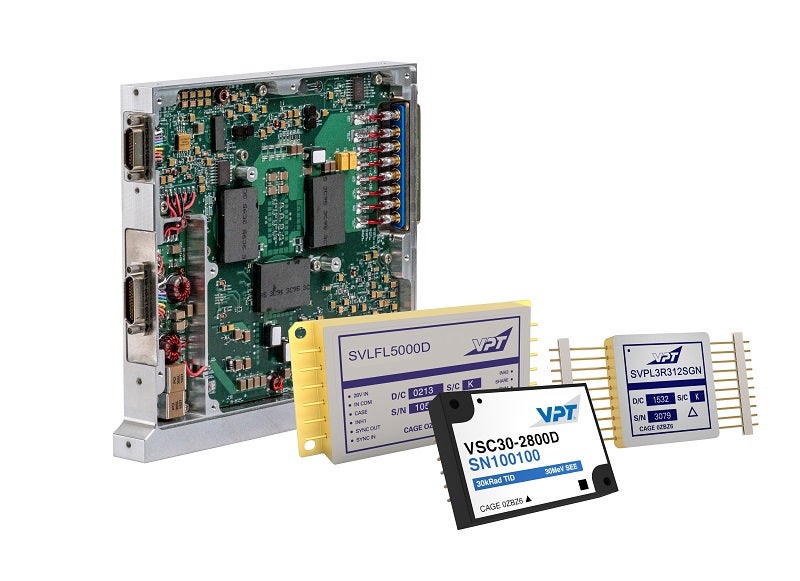
Radiation testing
Spaceborne electronics and components need to be robust and reliable, which require testing by experts with specialized equipment. VPT’s sister company, VPT Rad, provides these services at their radiation laboratory and test services facility.
Just north of Boston, Massachusetts, VPT Rad houses its state-of-the-art testing facility, that provides specialized environments and test solutions for evaluating electronics used in aerospace applications.
Providing both engineered and turn-key test solutions for Radiation Lot Acceptance Testing (RLAT), VPT Rad has a commercial laboratory that is approved by the Defense Logistic Agency (DLA) to perform radiation testing on electronic components. The independent radiation testing laboratory provides services for radiation test program planning, test execution, results evaluation, and complete DLA slash sheet reporting.
The facility features testing for both Low-Dose Rate (LDR) / TID and High Dose Rate (HDR) / TID gamma irradiation testing. It includes:
- In-house Cobalt-60 irradiators optimized for TID
- NIST certified traceable alanine dosimetry system
- DLA approved quality assurance program
- ESD protection program
- Comprehensive data analysis and reporting
Full turn-key service
Aridio Sanchez, President of VPT Rad, says that the facility offers a unique end-to-end service. “The majority of facilities across the US are just providing the radiation sources – you have to bring your own resources to finish your test, which includes the hardware design, the data analysis, the data collection. What we do here is provide end-to-end solutions. You can give us your part, drop it off, and we’ll take care of the rest.”
Sanchez states that this difference sets them apart from other radiation test facilities. “We provide turn-key services. We do all the pre-electrical work; we do all the development work on our end. The radiation sources are here in-house. We’ll provide that, we’ll do all the pulse measurements, and we’ll also provide a complete data pack which we’ll render to the customer with complete analysis of the results and performance of the parts.”
Spaceborne electronics have a tough life. Sanchez points out: “As the technology changes, we are constantly investing in new test equipment to accommodate any deviations or implementations in product designs as time goes on.”
Both VPT and VPT Rad are leading the way in designing, testing, and manufacturing advanced, radiation-resilient components and power systems. Their pioneering work will keep satellites working in space for years to come.
Download the whitepaper on this page to find out how VPT and VPT Rad’s radiation-resistant technology can help you.