
A team of researchers from Australia’s RMIT University is using laser metal technology to develop parts for defence aircraft under a two-year project.
Led by professor Milan Brandt, the RMIT team is working in collaboration with RUAG Australia and the Innovative Manufacturing Cooperative Research Centre (IMCRC).
The technology can be used to build and repair steel and titanium parts for both existing aircraft and the newest F-35 Lightning II fleet.
Brandt said: “It’s basically a very high-tech welding process where we make or rebuild metal parts layer by layer.”
The laser metal technology works by feeding metal powder into a laser beam, which is scanned across a surface to add new material in a precise, web-like formation.
It can be used to 3D print new parts or to repair and modify existing parts with a bond that is as strong as, or in some cases stronger, than the original parts.
How well do you really know your competitors?
Access the most comprehensive Company Profiles on the market, powered by GlobalData. Save hours of research. Gain competitive edge.
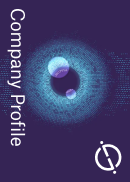
Thank you!
Your download email will arrive shortly
Not ready to buy yet? Download a free sample
We are confident about the unique quality of our Company Profiles. However, we want you to make the most beneficial decision for your business, so we offer a free sample that you can download by submitting the below form
By GlobalDataThe technology will help transform the supply of defence replacement parts by allowing parts to be easily built or repaired on-site instead of being stored and transported.
RUAG Australia Research and Technology head Neil Matthews said: “Instead of waiting for spare parts to arrive from a warehouse, an effective solution will now be on-site.
“For defence forces, this means less downtime for repairs and a dramatic increase in the availability and readiness of aircraft.”
According to RMIT, locally printed components would possibly save money on maintenance and spare part procurement, scrap metal management, warehousing and shipping costs.