General Atomics Aeronautical Systems (GA-ASI) has conducted fuselage structural integrity testing of its Certifiable Predator B (CPB) remotely piloted aircraft (RPA).
The new variant of Predator B RPA will be certified for flight according to the Nato Airworthiness Standard for unmanned aerial vehicle (UAV).
The testing involved determining the effects of airframe bending, aft section torsion, maximum power plant torque, multiple stress tests (load cases) on main and nose landing gear mounts, and maximum hoist load.
The proof tests validated the design of the new fuselage, which has been designed to meet lightning-strike, damage-tolerance, and turbulence-induced stress requirements.
The fuselage accommodates an integrated detect and avoid system, including an anti-collision radar system.
GA-ASI CEO Linden Blue said: "Completion of this testing signifies that the design of the new fuselage will be able to meet the strict requirements for type-certification and routine operations in national airspace."
How well do you really know your competitors?
Access the most comprehensive Company Profiles on the market, powered by GlobalData. Save hours of research. Gain competitive edge.
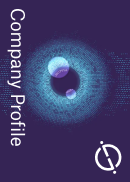
Thank you!
Your download email will arrive shortly
Not ready to buy yet? Download a free sample
We are confident about the unique quality of our Company Profiles. However, we want you to make the most beneficial decision for your business, so we offer a free sample that you can download by submitting the below form
By GlobalDataThe testing, which began in February at the company’s research and development facility in California, US, followed a two-day test readiness review (TRR).
Proof testing will be followed by aircraft flight testing this year, while the structural integrity testing of CPB’s wings and tail design was completed in December last year.
GA-ASI said that the proof testing allowed it to evaluate and confirm the integrity of CPB’s fuselage quickly and economically, enabling assessments of increasing mechanical stresses at levels higher than the airframe will incur in flight.
The resultant empirical data supports computational modelling, analysis, and verification to confirm compliance with exacting airworthiness requirements.
Data from the stress tests will be used for model correlation in order to maximise airborne safety.