
Given the difficulties in measuring the extent and value of reshoring, much of the debate about this topic is conducted on the basis of anecdotal evidence.
Swiss-based medtech company Ypsomed decided to reshore its insulin pen production in 2018 after more than 30 years in Mexico, in what is a classical example of a reshoring project to a high-labour-cost country made possible by highly automated production.
Similar examples of reshoring based on automated production processes are Sennheiser, a German manufacturer of microphones, which is reshoring production from China to Romania; Kemppi Oy, a Finish producer of welding equipment that reshored production back to Finland from India; and Gtech, a British vacuum-cleaner manufacturer that left China in 2019 to return to the UK.
What do reshoring companies have in common?
What are the common features of all these cases, and what conclusions can we draw from them?
The automation and robotisation of production processes is one of the key enablers for bringing production back to Europe and North America. While there is some variation in the figures cited for ‘operating cost per hour of a robot’ and ‘hourly wage costs’ (obviously depending on the country in question, the industry concerned, as well as the complexity of the processes), it is nearly always an order of magnitude of difference – an effect that is only going to get more pronounced over time.
With the cost of industrial robots, the periphery and set-up teach-ins are going down, while wage costs are going up with each collective bargaining round. With wage costs not being the main cost element any longer, there is no reason why production shouldn’t be close to where the demand is (Europe or the US).
How well do you really know your competitors?
Access the most comprehensive Company Profiles on the market, powered by GlobalData. Save hours of research. Gain competitive edge.
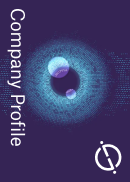
Thank you!
Your download email will arrive shortly
Not ready to buy yet? Download a free sample
We are confident about the unique quality of our Company Profiles. However, we want you to make the most beneficial decision for your business, so we offer a free sample that you can download by submitting the below form
By GlobalDataHow to measure reshoring
Maybe the most common approach to date when it comes to measuring reshoring are surveys and anecdotal evidence. The obvious problem with this approach is the hit-and-miss-nature of anecdotal data. Statistical data also has its flaws – given that in balance of payment-based foreign direct investment data in most countries we miss smaller capital movements (small and medium-sized enterprise investments) or effects such as simple relocations of machinery (which usually results in subsequent job creation). An alternative approach would be to look at trade data, especially if trade flows reverse, which would indicate major changes in the location of value creation.
An interesting attempt to quantify this in a more systematic way is the annual Kearney Reshoring Index. Sadly this only looks at reshoring from 14 specific Asian countries to the US. Based on this index, it appears that a large number of US CEOs are contemplating reshoring, especially out of China, owing to the country’s current political situation.
The picture that is emerging is one of executives moving from merely contemplating shortening their supply chains to them taking concrete steps to bring production back to the company’s country of origin. This effect is obviously more pronounced with end-user goods, where proximity to the market is more important and the demand is less plannable than with semi-finished input goods of industrial processes. Reshoring also tends to be more prevalent with high-value goods, where long lead times translate into rapidly rising working capital positions in corporate balance sheets and in knowledge intensive, high-tech sectors where intellectual property protection acts as a further catalyst.
Interestingly, it is not merely the corporate sector pursuing this line of thought. Following the persistent shortages of drugs and protective equipment during the Covid-19 pandemic, the Environment, Public Health and Food Safety Committee of the European Parliament called for more self-sufficiency and independence within the EU from India and China, and urged the bloc “to find way[s] to restore pharmaceutical manufacturing in Europe”. Another example here would be the drive to establish a state-of-the-art semiconductor production scheme in Europe under the Important Projects of Common European Interest programme.
The political will for such changes is also apparent when looking at the study requested by the European Parliament (PE 653 626 – March 2021) examining the options for bringing reshoring production back to Europe, coming to the conclusion that reshoring will become more prominent, irrespective of whether the rivalry between the US and China leads to an unbundling of strategic value chains, or whether the EU manages to create a third pole in between the two powers. France, with its ‘Plan Nouvel R’ (Reindustrialisation, Relocation, Reliance) is supporting reshoring by investing millions of euros, while the Inflation Reduction Act in the US is committing several hundred billion dollars to doing the same.
We are witnessing a changing paradigm. Today, it is less the average labour cost per hour and rather the technical skills of your workforce (the ability to integrate robots into your production processes and run them efficiently) that will be a source of competitive advantage. Robots will define your cost structure more than being located in low-labour cost countries. With reshoring indices pointing to a growing relocation of production back to Western core markets, and there being a scarcity of land and talent in these locations, it is time to act before the stampede is about to begin.