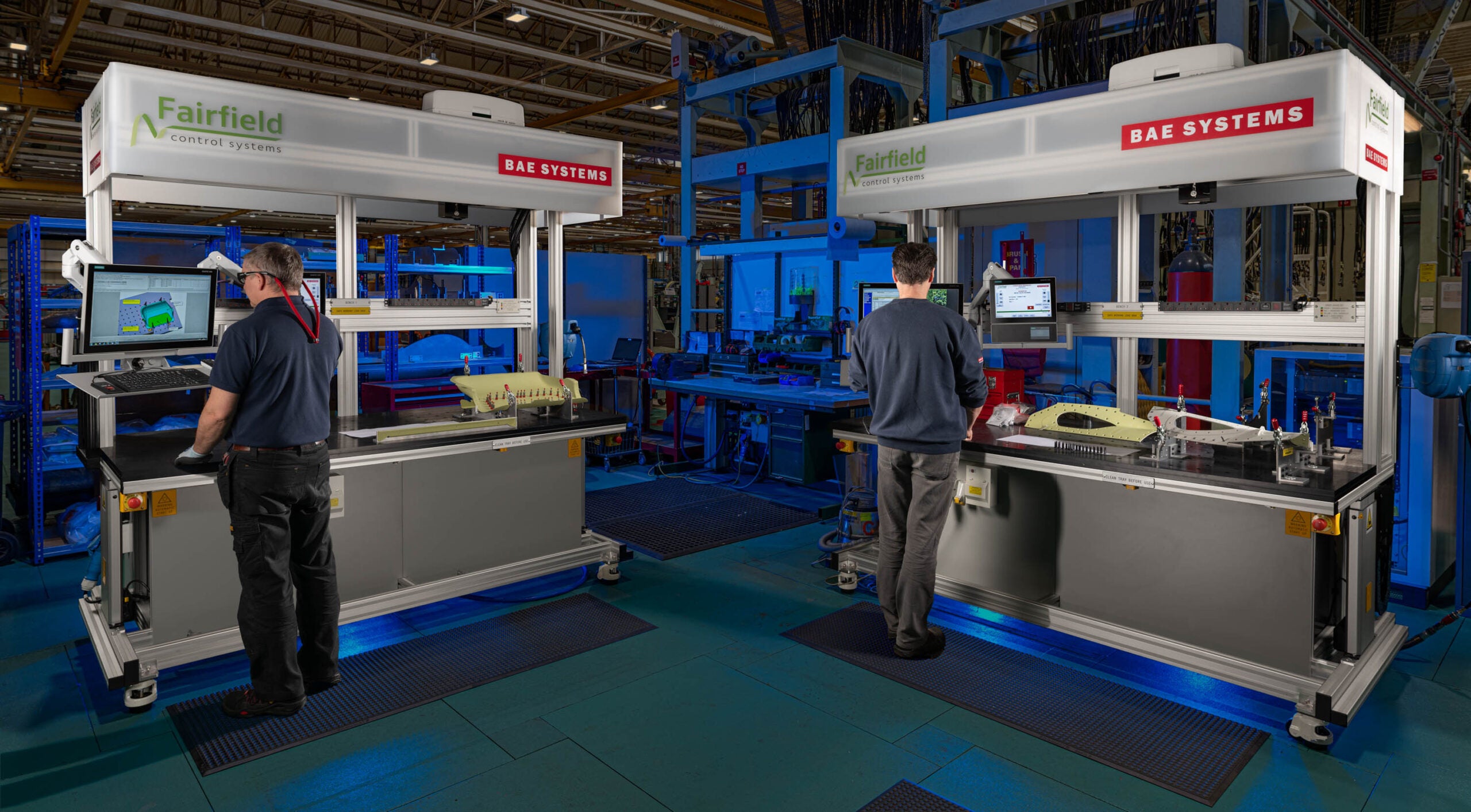
BAE’s Plan to Halve Aircraft Build Time and Reduce Costs
In an interview with Air Force Technology, BAE Systems Manufacturing and Materials Technology Director for the Air business, Professor Andy Schofield, said the company was looking to employ technological advances across the board in its quest to reduce the time and costs associated with building components, and complete air systems.
Schofield said: “We have a mantra of ‘halve the cost, halve [the] time’. We’re looking to reduce our engineering and manufacturing processes lead times and cost by half and that will result in a significant increase in our productivity.
“They are the challenges that we have within manufacturing which extends into our supply chain.”
Key to the BAE Systems Factory of the Future is the seamless combination of existing and groundbreaking technologies matched with new ways of working. The company is working hard to drive a transformative approach right across its supply chain, driving down lead times and ensuring the wider workforce are focused on adding value and embracing technologies to drive efficiency.
Part of this need for BAE, Schofield says, comes from the build rate difference between commercial and defence aviation, with the latter needing much more flexibility due to the typically lower build rate of fighter jets than passenger airliners.
Embedding advanced manufacturing technologies like additive manufacturing, robot-assisted assembly lines, intelligent logistics and autonomous robotics to boost productivity are all key to driving a more agile manufacturing capability to suit low and variable build rates.
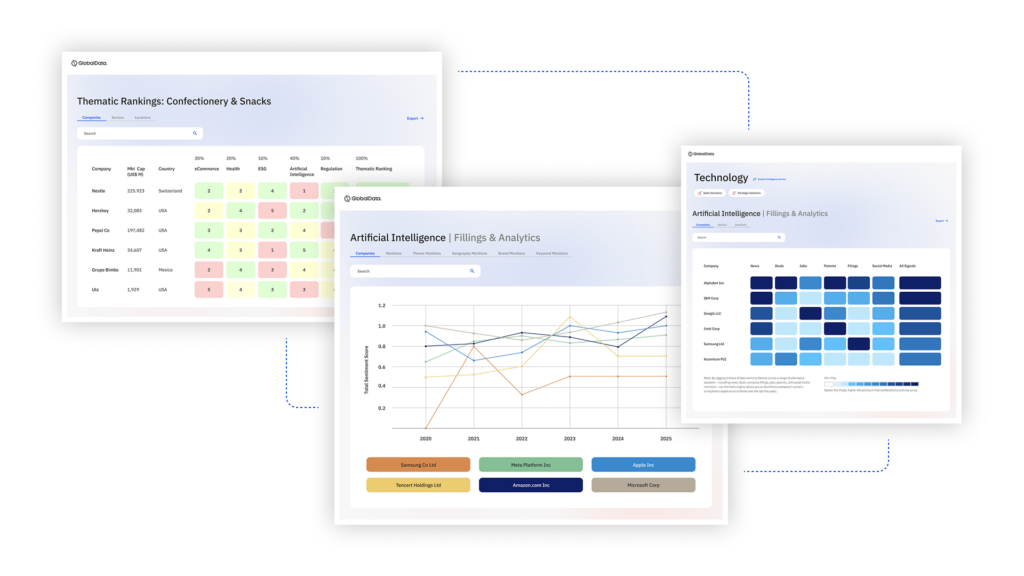
US Tariffs are shifting - will you react or anticipate?
Don’t let policy changes catch you off guard. Stay proactive with real-time data and expert analysis.
By GlobalDataA number of the manufacturing advances that will form the manufacturing solution for a Future Combat Air System (FCAS) are already reaching maturity according to Schofield, who cited the use of additive manufacturing of Typhoon components as an example of the technology in action.
Schofield said that one component currently flying on Typhoon aircraft is now additively manufactured from two parts when traditionally it was made from 16 parts.
Describing how digital manufacturing factors into the Factory of the Future, Schofield said the technology was of critical importance, particularly when it comes to achieving the flexibility in build-rates described earlier.
Schofield explained: “Digital manufacturing is critical; Intelligent Automation, the use of robotics and humans working together is really important. We need to replace the non-value-added, repetitive activities by the use of Intelligent Automation. This frees up the human operator to concentrate on more highly skilled tasks as a result.
“Moving parts around the factory using mobile robots is a significant enabler in the Factory and then we get into more detailed manufacturing processes such as additive manufacturing and metallic processes for joining, forming, and drilling holes, smart composite structures with embedded sensors and low-cost composite manufacturing.”
Image: BAE Systems.
BAE Systems believes that using these technologies – which often collectively come under the banner of ‘Industry 4.0’ – is an example of how the Company is embracing ‘fourth industrial revolution’ manufacturing innovations. Schofield added: “We’re starting to see some real breakthrough innovative manufacturing methods that haven’t been seen before.
“Factory of the Future provides a step-change in our manufacturing capability and we’re seeing some real breakthrough assembly methods and manufacturing methods coming to fruition.”
Typhoon, Tornado, F-35: Lessons from the past
Schofield said. “Every single project that we’ve introduced over the last 50 years has always required, from a manufacturing point of view, some sort of physical demonstration that we need to put in place that enables us to prove that we can achieve what the requirements of the project are.”
Like advancements in titanium machining needed for Tornado, or composite material development needed for Typhoon, Tempest is no different. Schofield explained: “When we look at the challenges that Tempest gives us, then we start to translate that challenge into what it really means from a manufacturing point of view.
“The whole Combat Air Strategy sets out very clearly how the UK Government expect UK Industry to deliver capability and how we need to transform to deliver real value. It’s all about setting ourselves up for the future, it is all about continuing the years of experience we’ve had within the UK of designing and manufacturing fast jets. It is important that we set the future for the Typhoon replacement in 2035, what’s known as Tempest, and it’s also about creating a skills pipeline and sustaining highly skilled roles in the UK.”
From BAE’s perspective, the Factory of the Future is just as important as creating a skills base to also create what Schofield calls the ‘engineer of the future’, pivoting the workforce away from the traditional manufacturing operations towards more digitally focused tasks to work seamlessly with the technologies on hand.
Commenting on the wider aims of the Factory of the Future Schofield added that: “Linking the supply chain, linking with the talent pipeline, bringing early careers and influencing the supply chain in the UK with the right talent that needs to come through.” is also key to the concept’s success.
While Factory of the Future may be seen as closely tied to Tempest, the lessons from the concept are being watched closely across the company’s other divisions, with advancements
in aircraft development being followed for how they could be pulled through to improving operations across the group.
Image: BAE Systems.
Schofield added that ‘collaboration’ across the wider Tempest supply chain, be it international and regionally is important to developing an effective distributed manufacturing ecosystem.
Schofield added: “The wider Factory of the Future, for us, is not just the physical factory that we work in, but it’s more the framework and ecosystem that sits around it.
“By taking those technology themes and working very closely in collaboration with research partners, technology providers, SMEs, academia and research technology organisations, we have a very agile way of collaborating from big blue-chip companies down to SME and startups in the UK.”