
Operating on rugged terrain like that found in Iraq and Afghanistan presents a dilemma to modern armed forces. Vehicles must strike a balance between having the capability to meet ever-evolving combat requirements and the reliability to function effectively under hostile conditions.
The British Army has suffered some well-documented setbacks with military vehicles in Afghanistan. In May 2009, for example, the National Audit Office released a report (“Support to High Intensity Operations”) that called attention to the poor performance of the Vector light protected patrol vehicle, with suspension and wheel hub reliability deemed particularly unacceptable. The problem, said the report, was exacerbated by a shortage of spares to address technical issues.
The poor protection of the Snatch Land Rover, which has been described to the House of Commons as “a death trap”, has further damaged the confidence of the British Army in its vehicles. The Ministry of Defence (MoD) announced on 22 September this year that the Snatch would be replaced by the better-armoured Ocelot light protected patrol vehicle, which should come into service in 2011.
A number of co-operating partners, including BAE Systems, Rolls-Royce, Thales, Boeing and Cranfield University, are responding to the issue of vehicle maintenance with the development of a new system called integrated vehicle health management (IVHM), which aims to combine a range of diagnostic tools within a single platform for vehicles on land, in the air and at sea.
The system will be able to intelligently monitor vehicle functions and pick out faults in the earliest stages, which should allow engineers to rectify them before parts need to be replaced. The overall objective is to extend vehicle reliability, reduce through-life costs and minimise the number of vehicles rendered unavailable by irreparable technical problems.
Integrating diagnostic tools
How well do you really know your competitors?
Access the most comprehensive Company Profiles on the market, powered by GlobalData. Save hours of research. Gain competitive edge.
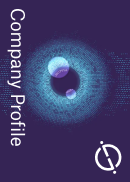
Thank you!
Your download email will arrive shortly
Not ready to buy yet? Download a free sample
We are confident about the unique quality of our Company Profiles. However, we want you to make the most beneficial decision for your business, so we offer a free sample that you can download by submitting the below form
By GlobalDataThe IVHM system, which BAE expects to be in use across UK military vehicles within the next five to ten years, aims to provide military maintenance staff with a comprehensive and user-friendly diagnostics system by combining sensors with advanced diagnostic software.
Peter Foote, executive scientist at BAE Systems and one of the principal figures behind the development of IVHM, explains the system and its appeal. “IVHM works by linking sensors and other sources of data that monitor components, subsystems and systems with software tools able to diagnose and in some cases predict the ‘health’ of those systems,” he says. “This health information is then fed into logistic and asset management systems allowing proactive and pre-emptive rather than reactive maintenance. The health status information can also be used for improving the real time picture available to mission controllers and operators of asset status.
“The key word is ‘integrated’,” he says. “The advances in information and sensor technologies have opened the door to joining up existing monitoring capabilities with the diagnostics and platform support processes resulting in a whole greater than the sum of the parts.”
The IVHM concept features a wealth of technology. In addition to fault sensors built in to vehicle structures to provide constant monitoring, the system includes BAE’s corrosion monitor system, which gives early warning of corrosion by measuring corrosive damage to the sensor, which degrades faster than the structure to which it is attached. The corrosion monitor system is currently being trialled in the field on the British Army’s Warrior vehicles.
Another sensor system being trialled for inclusion in the IVHM package is acoustic crack detection. Already tested on Hawk combat aircraft, these sensors measure small sounds made as a crack emerges and grows to give advanced warning to engineers.
Feedback from sensor systems like these will be analysed by a software package called intelligent fault diagnosis technologies (IFDT), which is the intelligent link between the sensors and operator. Using mathematical algorithms, the software can convert raw diagnostic data into an actionable list of probable causes.
As IFDT accumulates successful confirmed diagnoses, this “experience” informs future processes, meaning that the software becomes more intelligent over time. IFDT is being trialled on the Tornado fighter.
Foote notes the challenge of creating a system that pulls together such a diverse range of technology into a useful whole. “The big challenge is managing potentially large amounts of diverse data and converting this efficiently into consistent, actionable information – for example maintenance actions,” he says. “Also, defence platforms have myriad legacy support systems – IVHM must be able to operate within those existing infrastructures while delivering its benefits.”
Contracting for availability
One of IVHM’s most important roles for the defence industry is as an enabler for an increasingly popular trend in equipment contracting – contracting for availability. Under this new arrangement, contractors sign deals with armed forces based on the guaranteed availability of an agreed number of vehicles. Instead of manufacturers simply supplying vehicles and then selling maintenance and spares when problems occur, contracts provide a comprehensive service that guarantees that vehicles are available for operations, with financial penalties and incentives to enforce the guarantee.
The thinking behind this shift from traditional contract set-up for military vehicles is to maximise platform availability and shift the maintenance risk from national defence organisations to the industry that supplies them. The hope is that it will lead to more cost-effective procurement (as more budget costs will be fixed rather than buckling under the weight of additional maintenance fees) and more reliable vehicle fleets.
An early prototype for the contracting for availability trend, ATTAC (availability transformation: Tornado aircraft contract), was signed by BAE and the MoD in December 2006 after a number a number of interim maintenance deals. Worth £947m, the contract placed the responsibility for the availability of the Royal Air Force’s Tornado fleet (GR4 and F3) in BAE’s hands up until 2017.
According to BAE, ATTAC has been a great success so far, with the company stating that the deal will save the MoD more than half a billion pounds over the initial ten-year phase of the programme. Targets such as 85% for line replaceable items to be exchanged within one hour are being met (and in this case, exceeded) and MoD savings are being achieved across many areas.
Developing and implementing the IVHM platform could be a key component in the proliferation of the contracting for availability model for platforms on land, in the air and at sea. If the defence industry is to be incentivised to provide clients with comprehensive “depth support” agreements, it is important that technology exists to allow companies to properly monitor the health of vehicles.
For this purpose, IVHM is the technology that the likes of BAE, Thales and Boeing are throwing their weight behind. Despite the potential complications that contracting for availability could bring to the defence contracting landscape, there are significant advantages for both industry and military operations if it becomes a successful model. As well as providing military personnel with a new tool to ensure the operational reliability of their vehicles, IVHM could also help usher in a new era of defence procurement.