
Visit our Covid-19 microsite for the latest coronavirus news, analysis and updates
Follow the latest updates of the outbreak on our timeline.
Lockheed Martin is taking measures to mitigate Covid-19 impacts on F-35 production and rapidly recover from the pandemic, by adjusting work schedules, maintaining employee skillsets and accelerating payments to suppliers.
The latest move comes in response to previously reported F-35 supplier delays due to the outbreak.
Lockheed Martin and the International Association of Machinists and Aerospace Workers (IAM) have reached an agreement to temporarily commence alternate work for F-35 production line employees in Fort Worth, US, to maintain their workforce.
The new schedule will be operational from the following week and will be divided into shifts with three groups in each shift.
How well do you really know your competitors?
Access the most comprehensive Company Profiles on the market, powered by GlobalData. Save hours of research. Gain competitive edge.
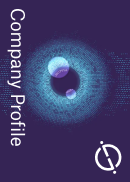
Thank you!
Your download email will arrive shortly
Not ready to buy yet? Download a free sample
We are confident about the unique quality of our Company Profiles. However, we want you to make the most beneficial decision for your business, so we offer a free sample that you can download by submitting the below form
By GlobalDataThe groups are planned to work on rotation for two weeks. The schedule will continue for its first three-week cycle.
During the three-week work schedule, the company will compensate employees working for 96 hours or more with an off while giving them full pay.
The new schedule will permit Lockheed Martin to staff the production line, meeting the workflow resulting from supplier delays.
Additionally, it will provide an opportunity to adjust work to better support production.
Lockheed Martin Aeronautics executive vice-president Michele Evans said: “These are challenging times, but managing tough challenges is when the F-35 programme performs at its best.
“The alternate work schedule maintains the specialised skillset of the employees and provides opportunities to for us to adjust our workflow to account for supplier delays due to Covid-19.
“Our F-35 workforce is the best in the world at what they do, and we will continue to deliver on our customer’s mission.”
The company will alter the work schedule as per further business requirements.