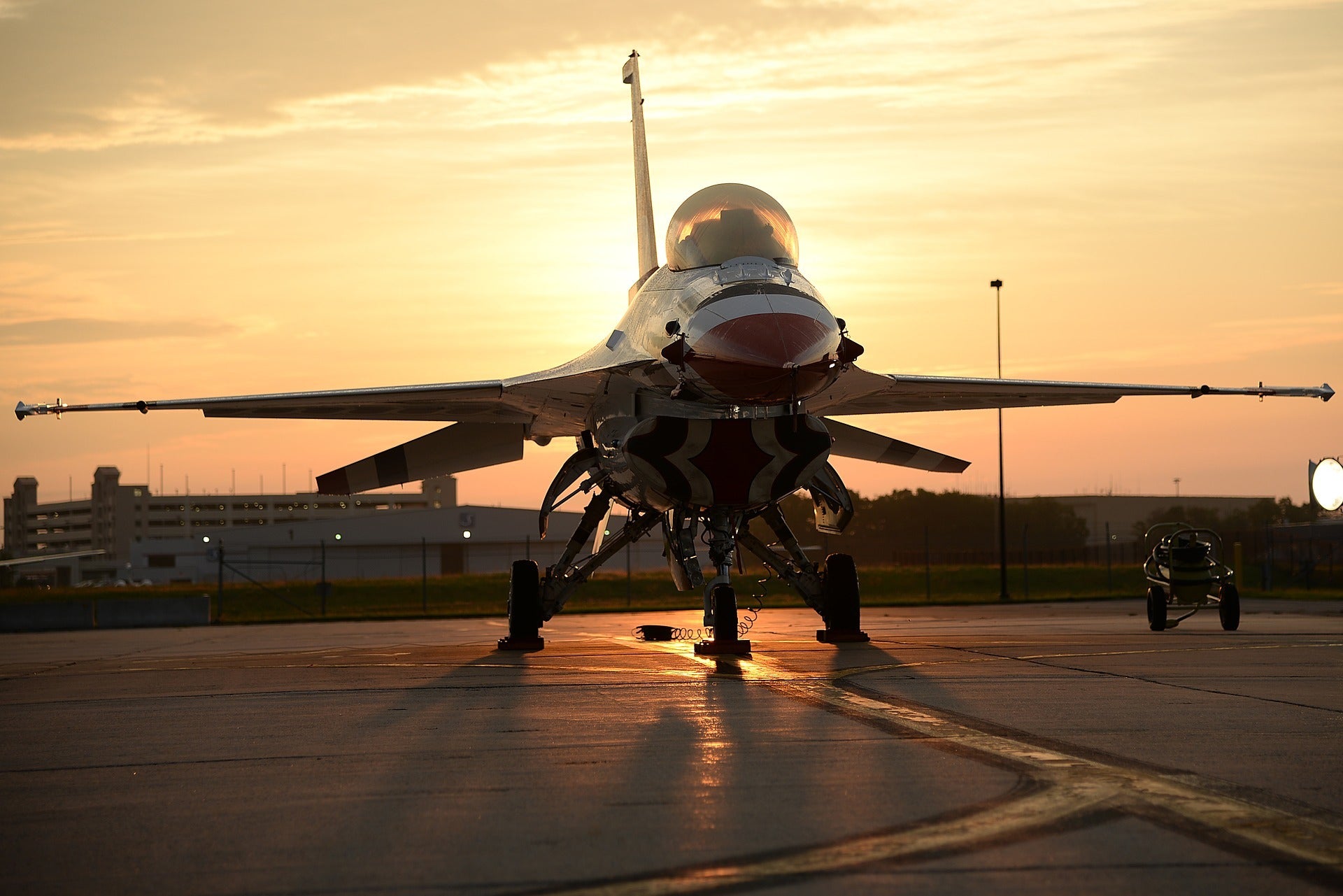
Optomec has received a process development contract for additive manufacturing (AM) repair of F-15 and F-16 fighter jets’ engine components.
The US Air Force Sustainment Center at Tinker Air Force base (AFB) awarded the $500,000 contract.
The solution for repairing the jet engine components will depend on Optomec’s LENS technology.
The company’s LENS technology is a 3D metal AM technique based on powder-fed Directed Energy Deposition (DED).
It also relies on advanced vision and distortion compensation software and other proprietary enabling machine capabilities.
The company noted that repairs must be conducted in ‘oxygen-free environments’ to ensure ‘proper metallurgy and mechanical performance’.
How well do you really know your competitors?
Access the most comprehensive Company Profiles on the market, powered by GlobalData. Save hours of research. Gain competitive edge.
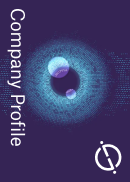
Thank you!
Your download email will arrive shortly
Not ready to buy yet? Download a free sample
We are confident about the unique quality of our Company Profiles. However, we want you to make the most beneficial decision for your business, so we offer a free sample that you can download by submitting the below form
By GlobalDataOptomec will create optimised process parameters and methods to aid the AM repair of titanium and nickel-base superalloy made turbine blades.
According to the company, these ‘printable recipes and libraries’ will be executed simultaneously with the delivery of an advanced automated Turbine Blade Repair machine.
The programme has a projected 184% return on investment (ROI) and a less than two-year payback period.
It is expected to save millions of dollars for the USAF, which maintains its fleet of over 5,000 aircraft.
Optomec Business Development vice-president Jamie Hanson said: “The turbine industry has already widely adopted Optomec’s automated DED solution for high volume nickel alloy repair of aviation parts; meanwhile Optomec has worked out the process recipes for titanium repair.
“This solution essentially takes Optomec’s titanium repair process to high volume levels where it will have a major impact on lowering maintenance costs as engine OEMs use more and more titanium.”
In the last two decades, the company’s AM repair processes have been used to repair more than ten million turbine engine components.