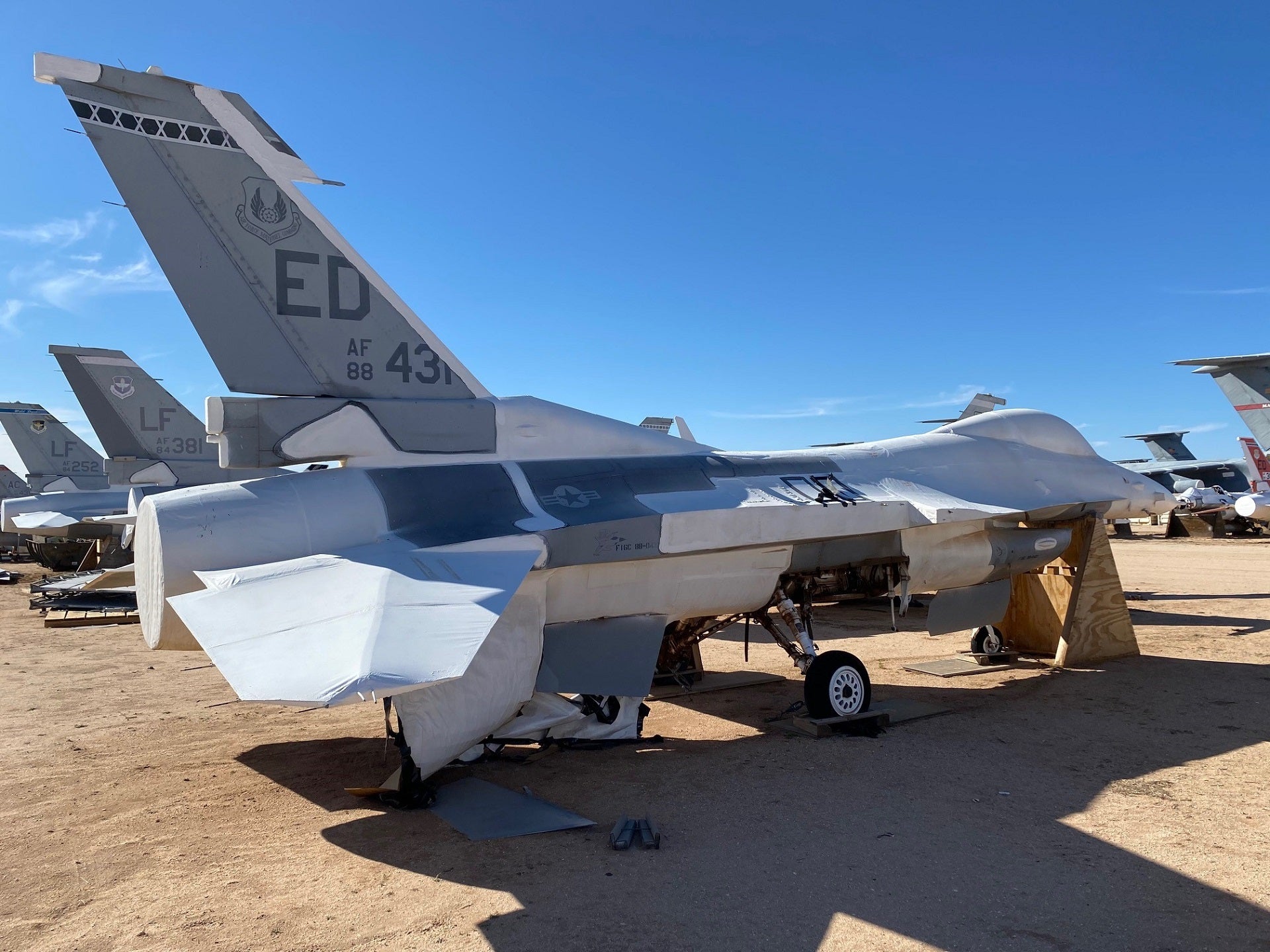
Wichita State University’s National Institute of Aviation Research (NIAR) has been awarded a contract to develop a digital twin of the US Air Force (USAF) F-16 Fighting Falcon fighter jet.
The F-16 is a fourth-generation aircraft manufactured by Lockheed Martin. The potential four-year project will support efforts for the future sustainment and modernisation of the jet.
Work under the contract involves disassemble and scan of two F-16s in storage at the 309th Aerospace Maintenance and Regeneration Group (AMARG) at Davis-Monthan Air Force Base, reports Brian Brackens.
F-16 Program Office Digital Twin program manager 1st lieutenant Connor Crandall said: “Our goal is to create a full-scale 3D model of the aircraft, with the exception of the engine.
“The data will be used to help address future parts obsolescence and mitigate supply chain risks because we won’t have to rely on legacy manufacturing sources and processes.
“We’ll have the 3D models, and designs that we can send to the manufacturers we choose.”
The project is expected to result in saving time and sustainment costs for the USAF.
The disassembled aircraft will be transported to Wichita, which is expected to be completed by 30 September.
NIAR will be responsible for developing 3D models of the aircraft’s environmental control, hydraulic and fuel systems.
NIAR F-16 programme manager and sustainment director Dr Melinda Laubach-Hock said: “Developing a virtual engineering environment that integrates structures and systems components will provide a virtual test bed for future modifications and other sustainment actions prior to physical implementation.
“Virtually testing prior to implementation will streamline the process, reduce airframe downtime, and increase mission readiness of this key military asset.”